The Oil Drum Kiln:
Make it – pack it – burn it
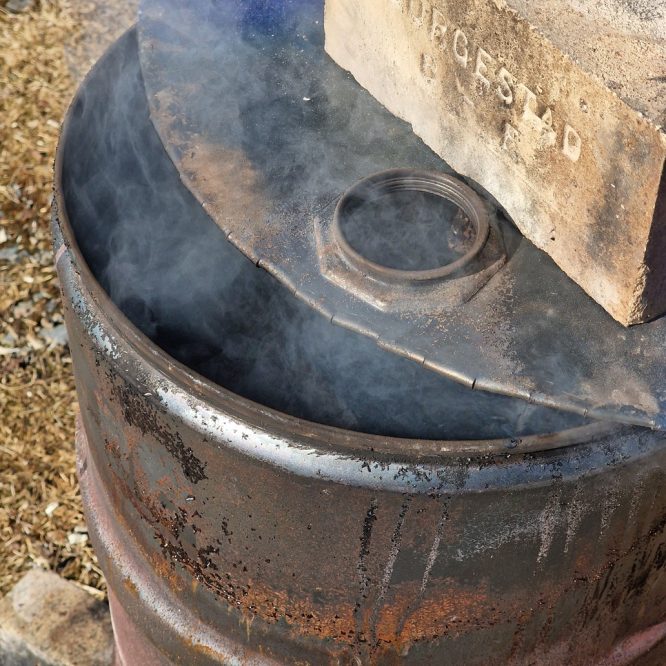
Also check out this article:
First some practical advice on making the oil drum kiln, later in the article, how to fire it:
The easiest way to get the lid off an oil drum is with a wide hammer and a wood chisel. It sounds like the wrong tool, yes, it’s a woodworking tool, and the chisel needs some serious sharpening afterward. But this works better than both a sheet metal shear and an angle grinder.
Whatever tool you use, the cut will be as sharp as a knife blade. Use the sheet metal shear to cut many 1 cm deep “teeth”, and bend each sharp “tooth” back; now the outer edge is less sharp. This lid is from a bigger oil drum and are needed to close down the fire.
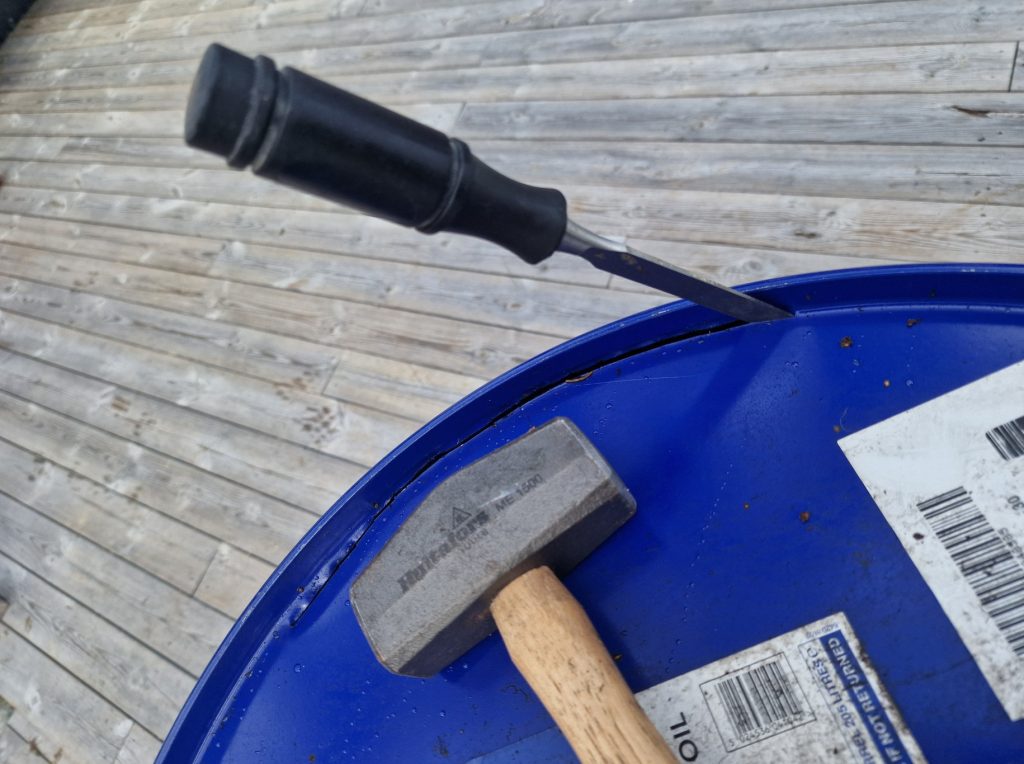
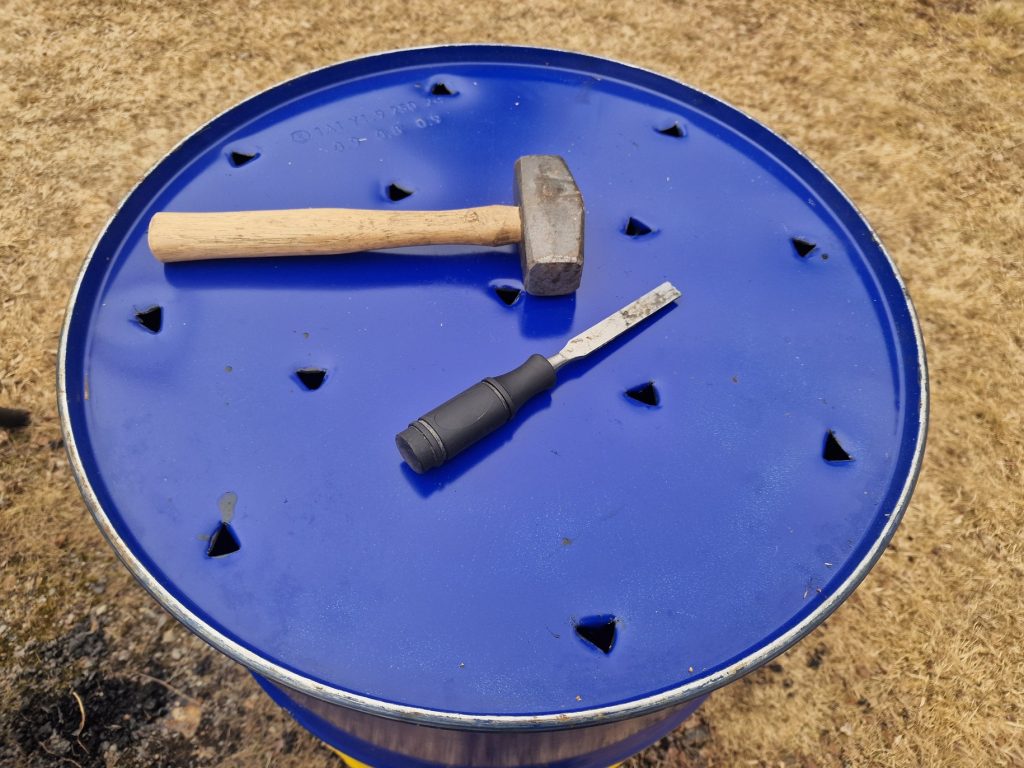
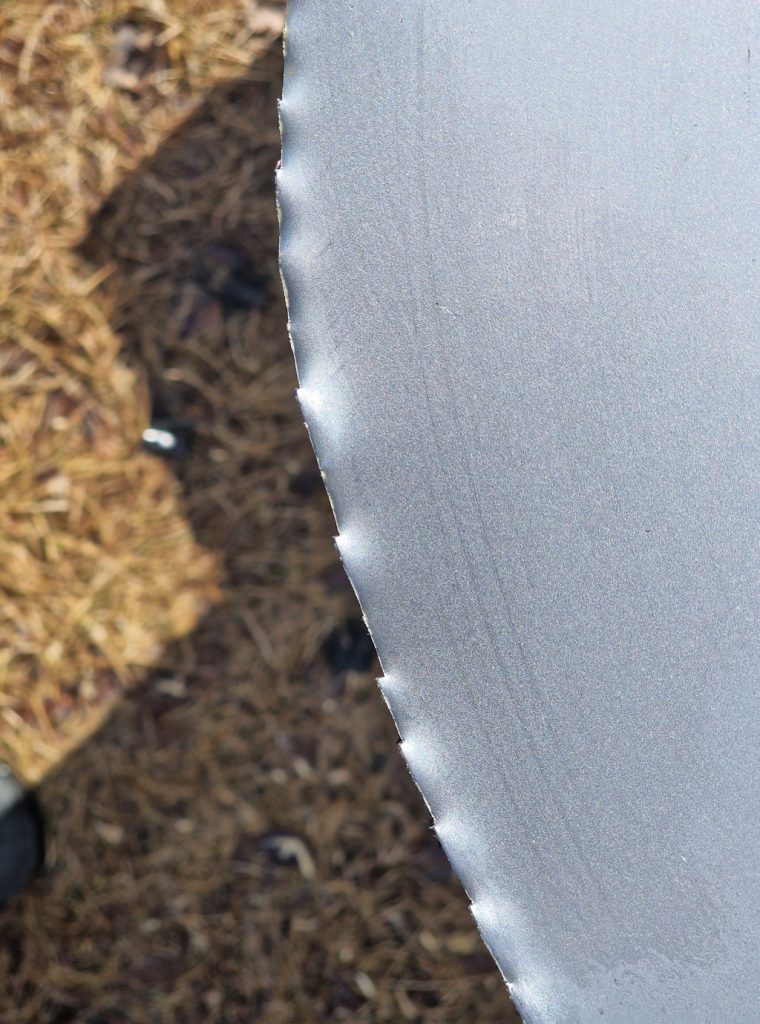
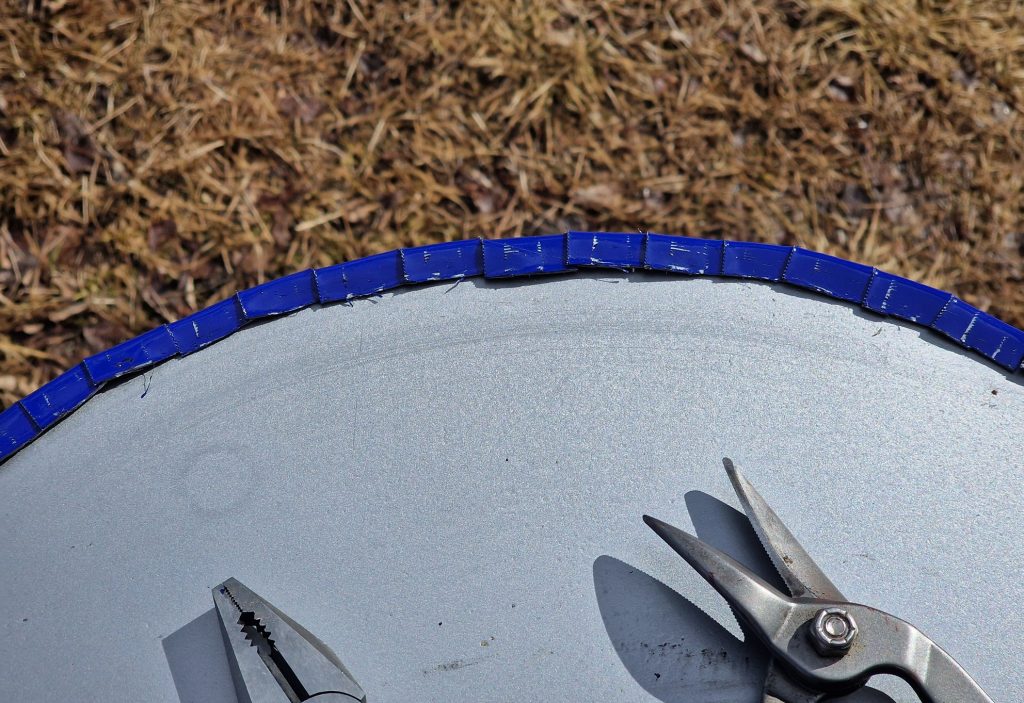
Pour out ALL the oil left in the oil barrel before start firing!
Burn it out is not a good idea. Some oil doesn’t burn in itself; it won’t burn without a wick, and if you make a “wick”, it burns like a candle forever. Oil starts to boil at 200 – 300 degrees Celsius. Burning oil bubbles like boiling water, but it’s 300 °C.
If the oil drum contains both water and oil, it’s just not possible to burn the oil drum kiln free from oil.
I regret! This soup of wood, oil, water, and paper will just never burn away.
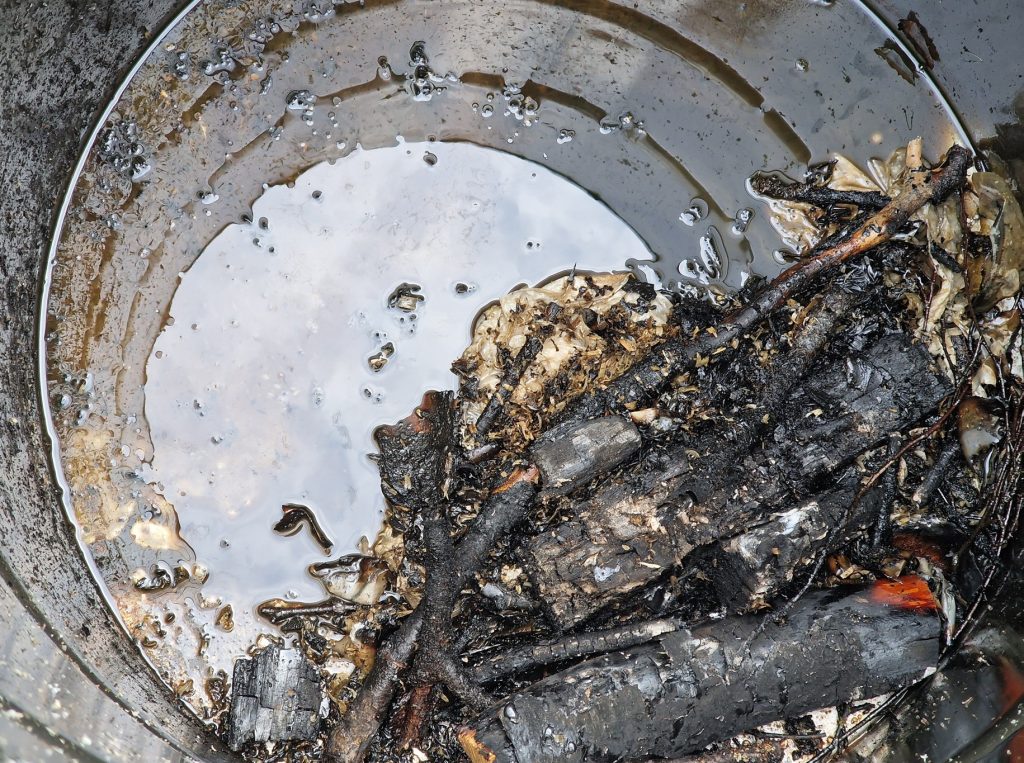
When empty the steel drum for oil and the ventilation triangles are made, fill it up with dry clay vessels, sawdust, wood, and wood pellets.
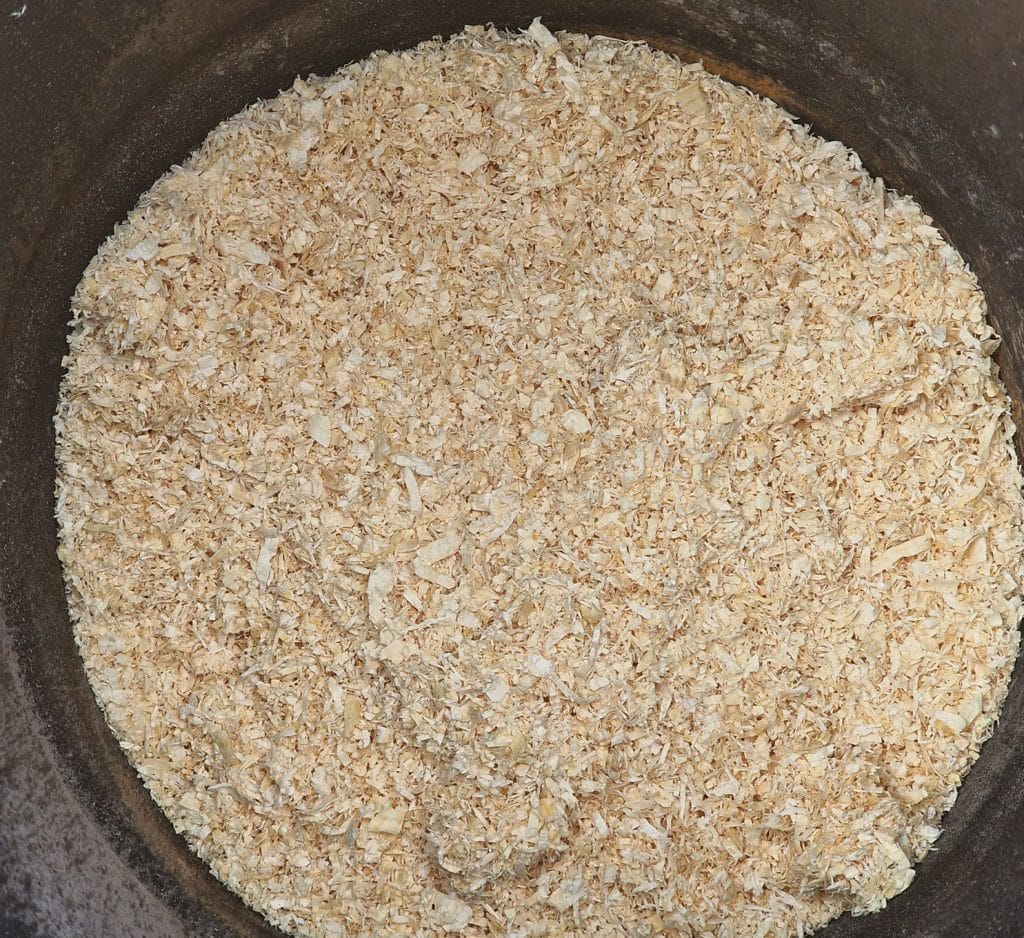
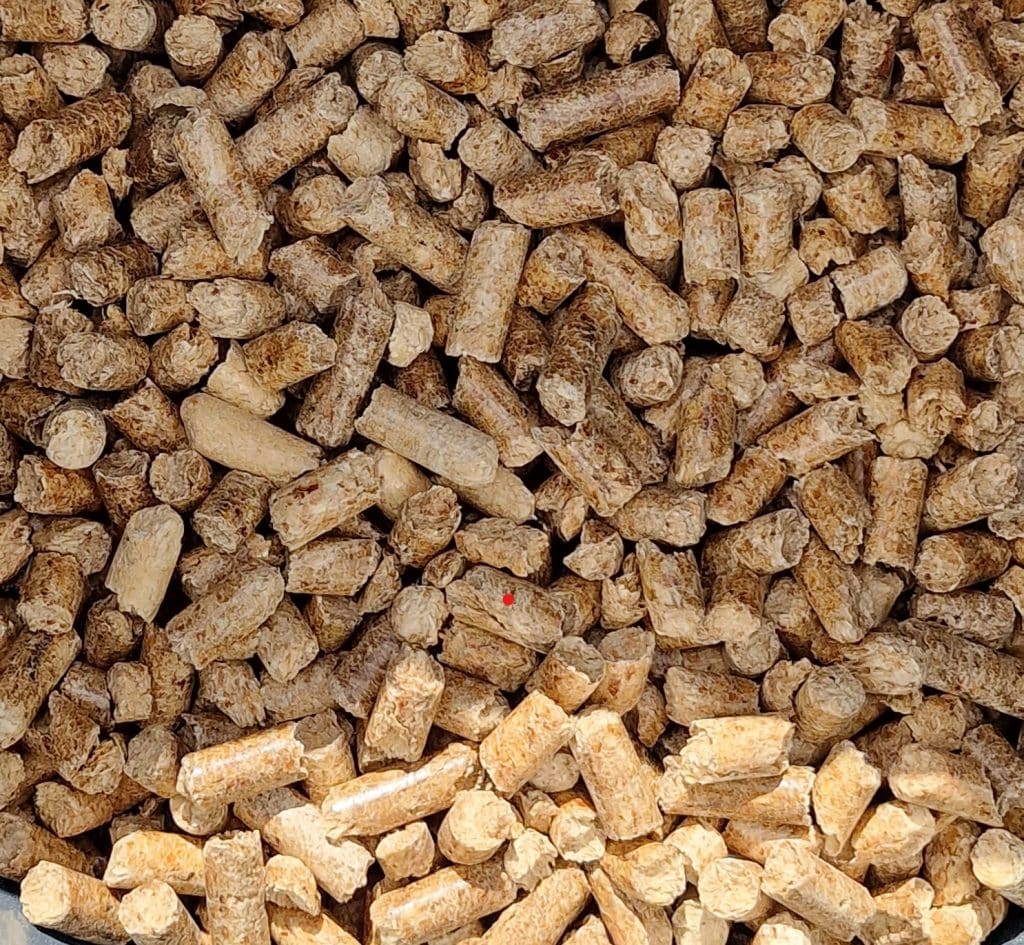
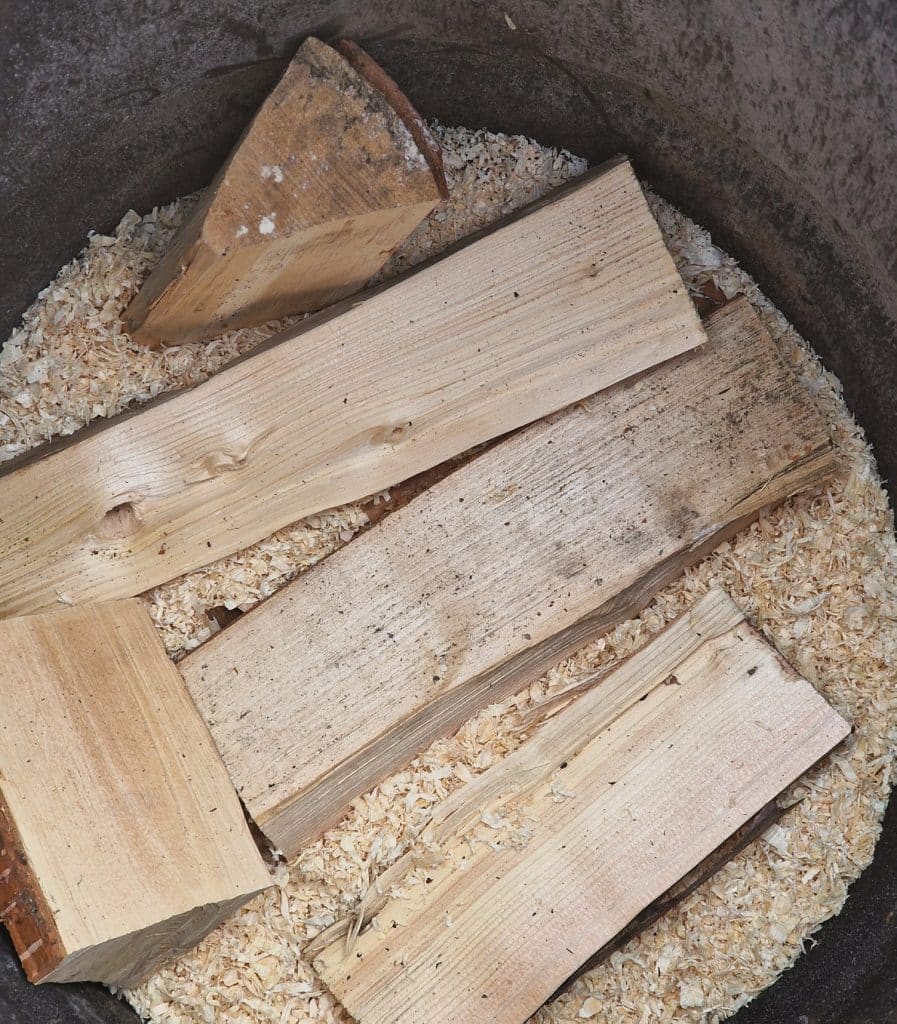
I put the clay in the center of the steel drum, covered with a good layer of sawdust above and under. I have not found the best way to distribute the fuel yet, but I put wood at the bottom, and the top 10 cm I use sawdust:
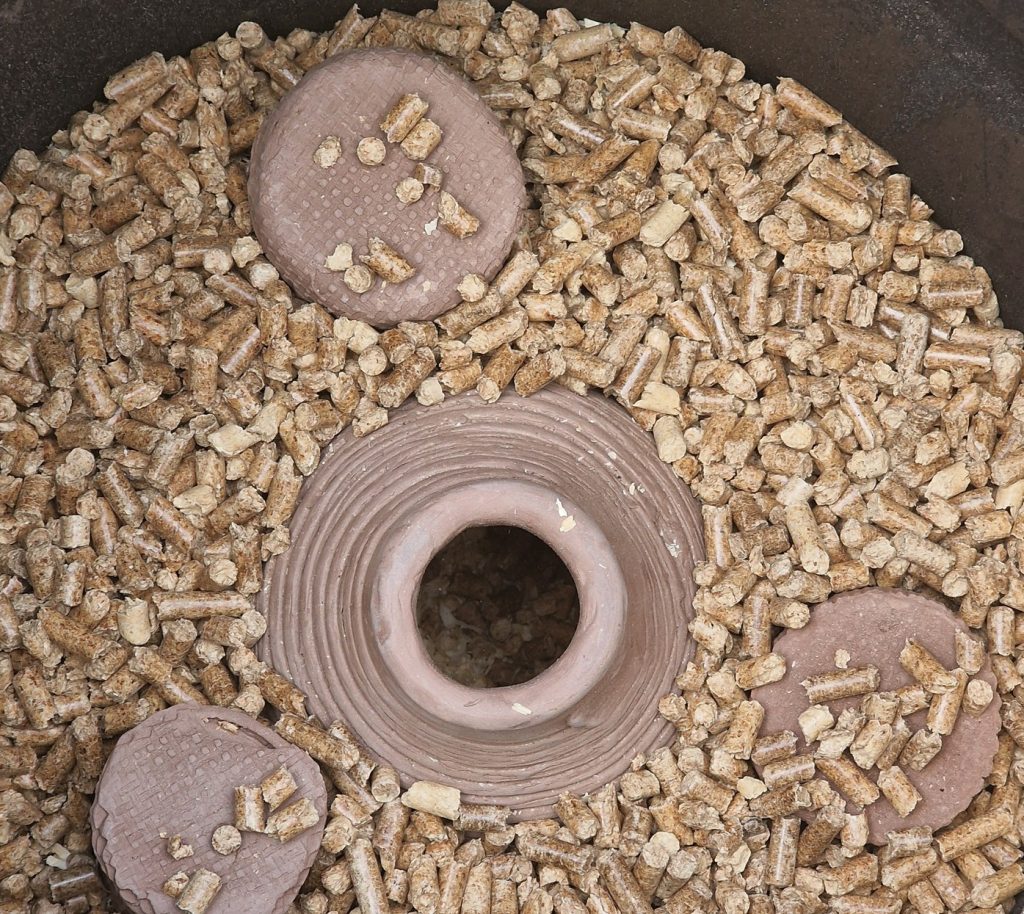
Ignite the kiln and let it burn with open flames for an hour.
Now it’s hot enough to continue to burn when you put the lid on:
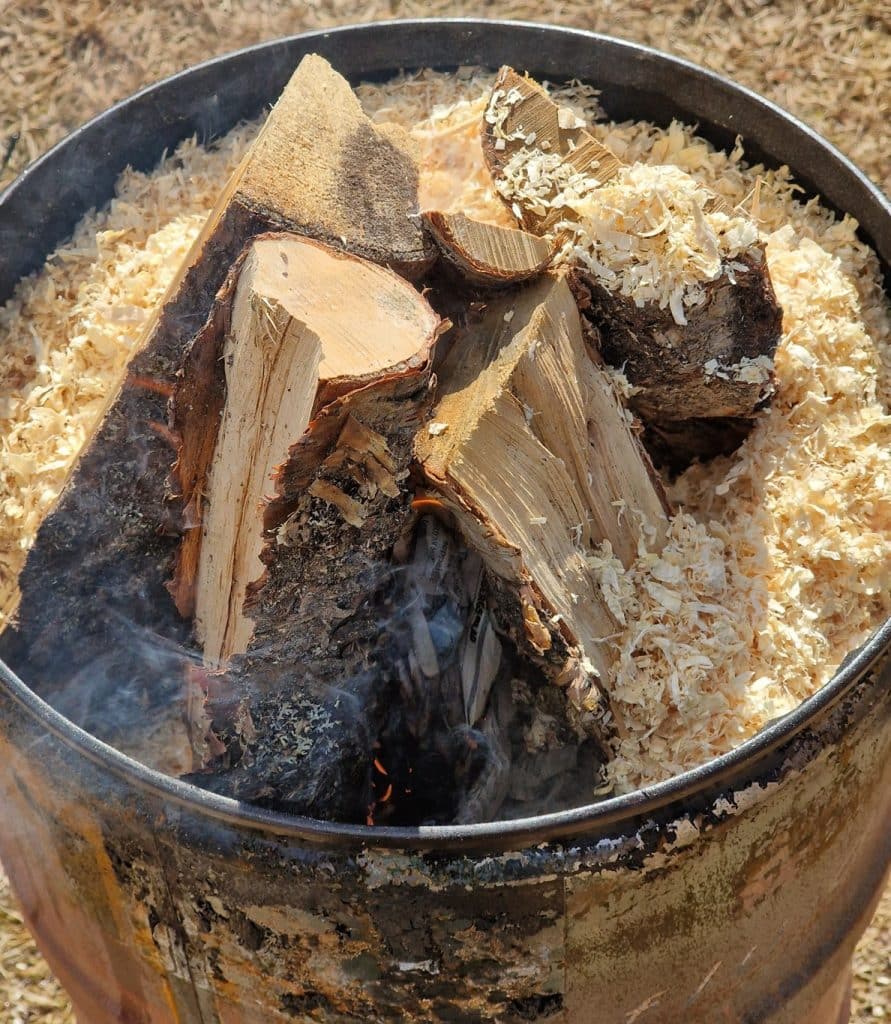
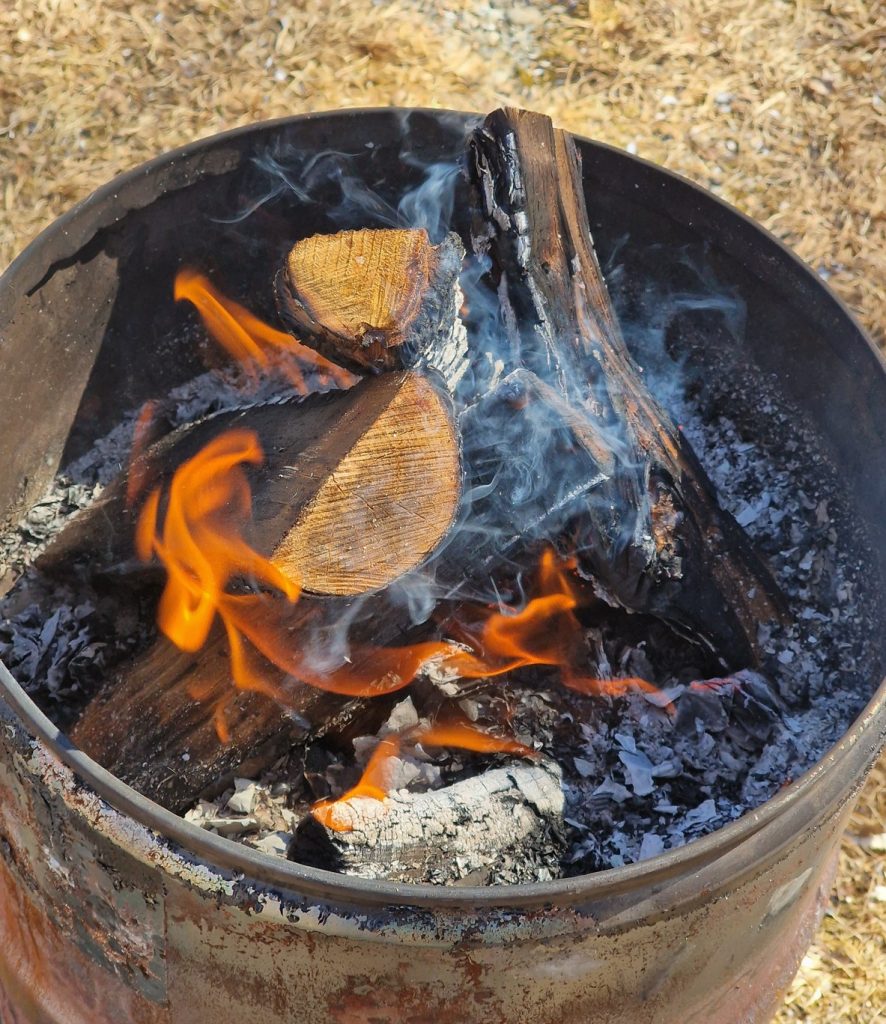
Smoke Smoke Smoke – 10 hours of white smoke. The sawdust kiln burns slowly and quietly with a thin line of smoke:
- Black smoke means the fire has too little oxygen; large amounts of unburned carbon particles are present in the incomplete combustion
- No smoke means optimal combustion
- Gray smoke means a fire between those two stages
- White smoke is associated with moisture and wet wood
From the beginning to the end it burns with gray smoke, I would almost say white, but this is dry wood. When put on the lid, the fire gets suffocated, we want it to burn with a minimum of oxygen so we get black sooted ceramics. But the smoke never turned black like we could expect.
Almost choke the fire, but if the oxygen supply is closed down too effectively, the fire will stop.
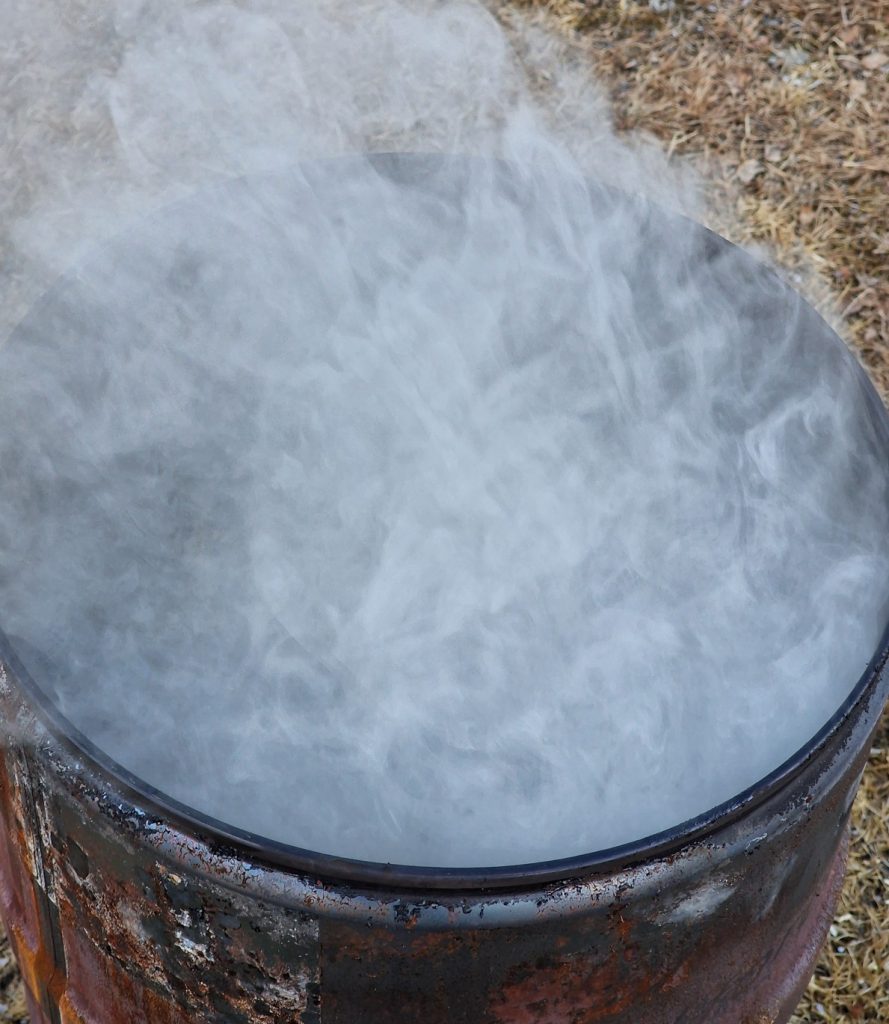
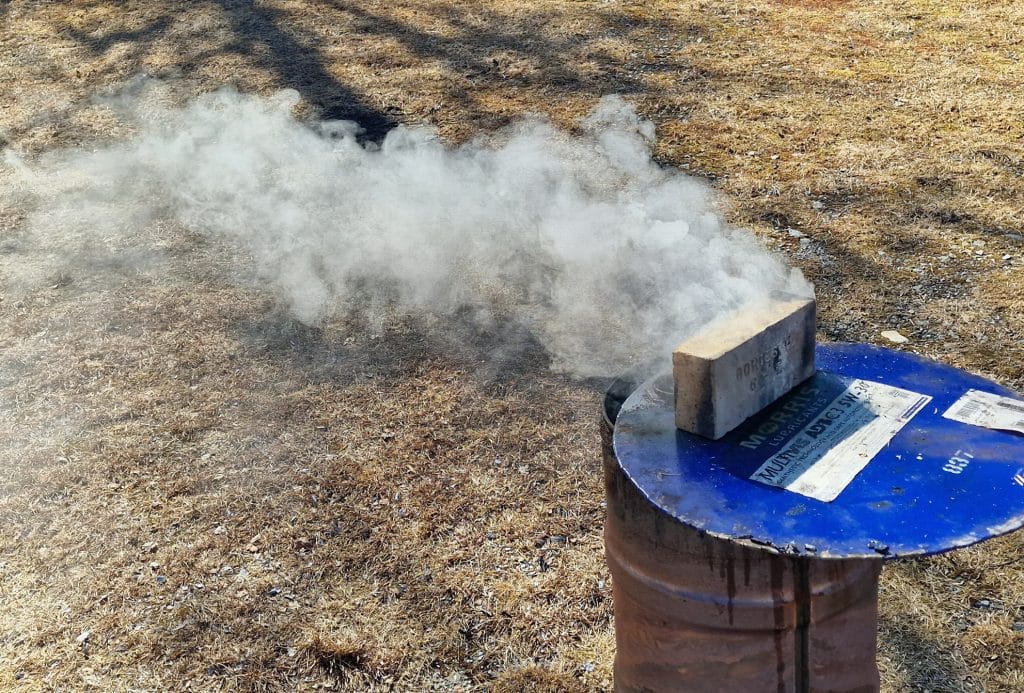
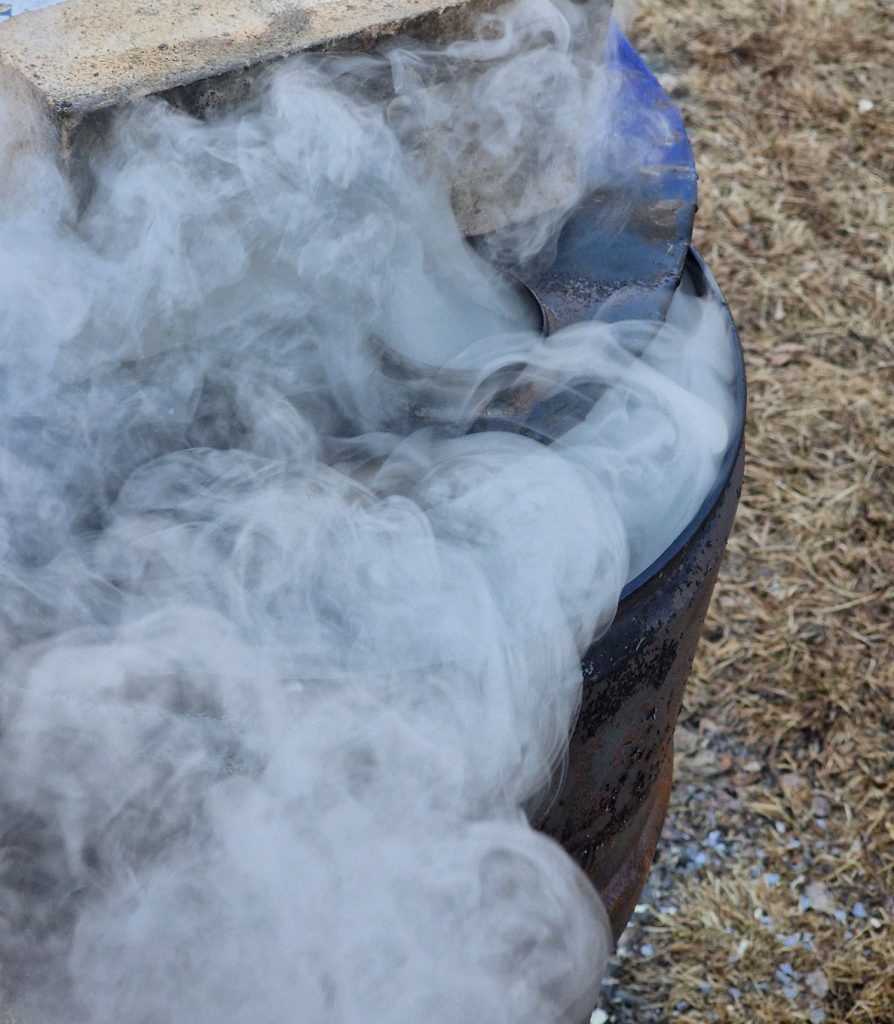
After some hours, pieces of burning sawdust fall out from underneath the oil drum, which means the fire has reached the bottom of the oil drum:
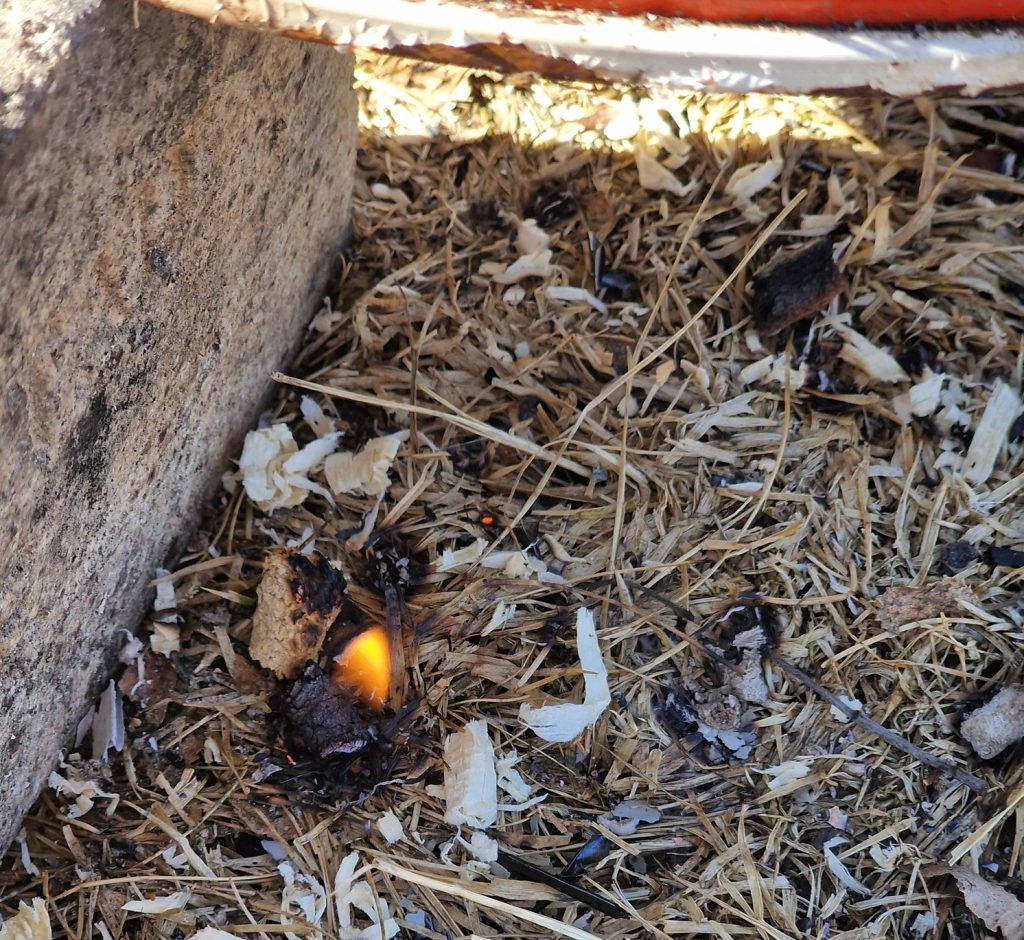
The firing hour by hour:
13.30 Starting the fire on top of the oil drum and letting it burn for an hour
16.00 Partly close the top of the oil drum with a lid
17.00 Burning sawdust falling out of the ventilation at the bottom
18.00 Smoke coming out is no longer hot, high temperature deeper in the oil drum
18.15 Close the lid, now it only comes smoke out of the cork hole
21.00 The smoke stopped, but it’s glowing hot deep inside the oil drum kiln
08.00 Next morning: Smoke rising from the ash, there is still a little heat left
Next day – The pottery:
Not what I expected! But it was only a test; 3 out of 4 vessels survived, the largest vase about 20 cm without chamotte cracked (not surprisingly, but it seems to “almost” made it). It seems like the first part of the firing was under heavy reduction, with black soot still on the inside of the steel wall and the top of the vase. Then the fire burned its way down to the air vents at the bottom and opened up a flow of air. When the air was no longer absent, the fire and the clay re-oxidised.
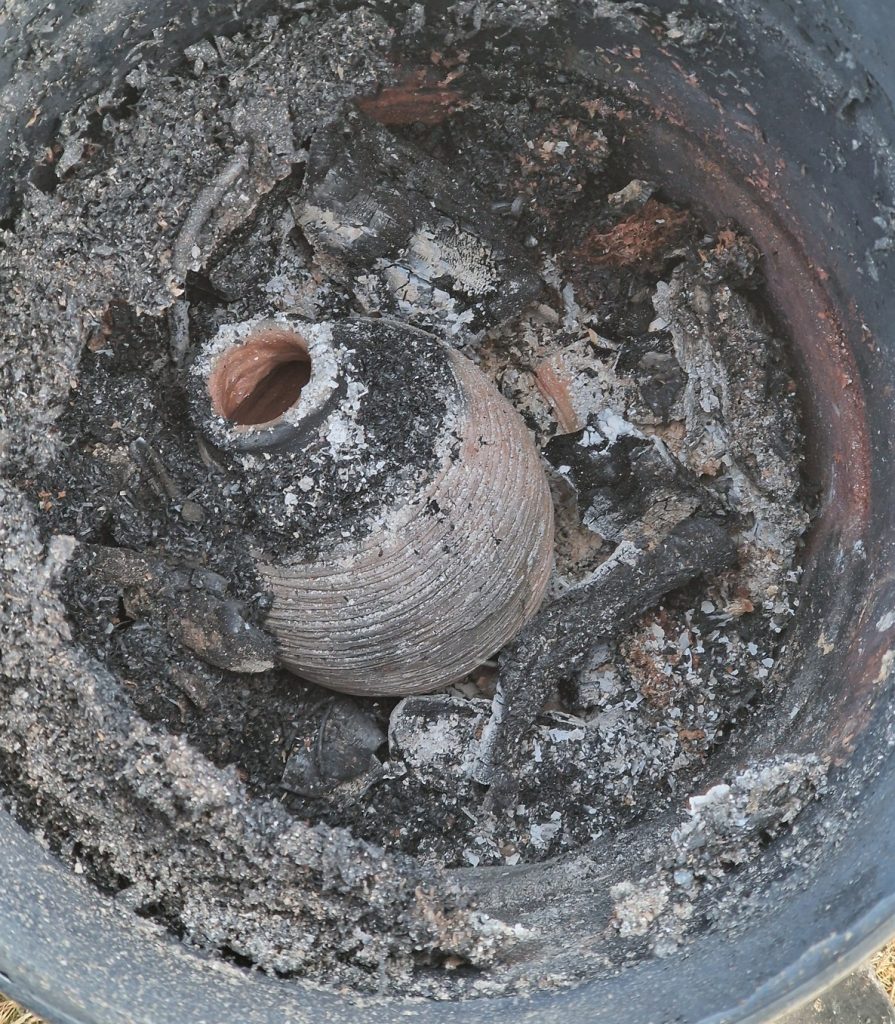
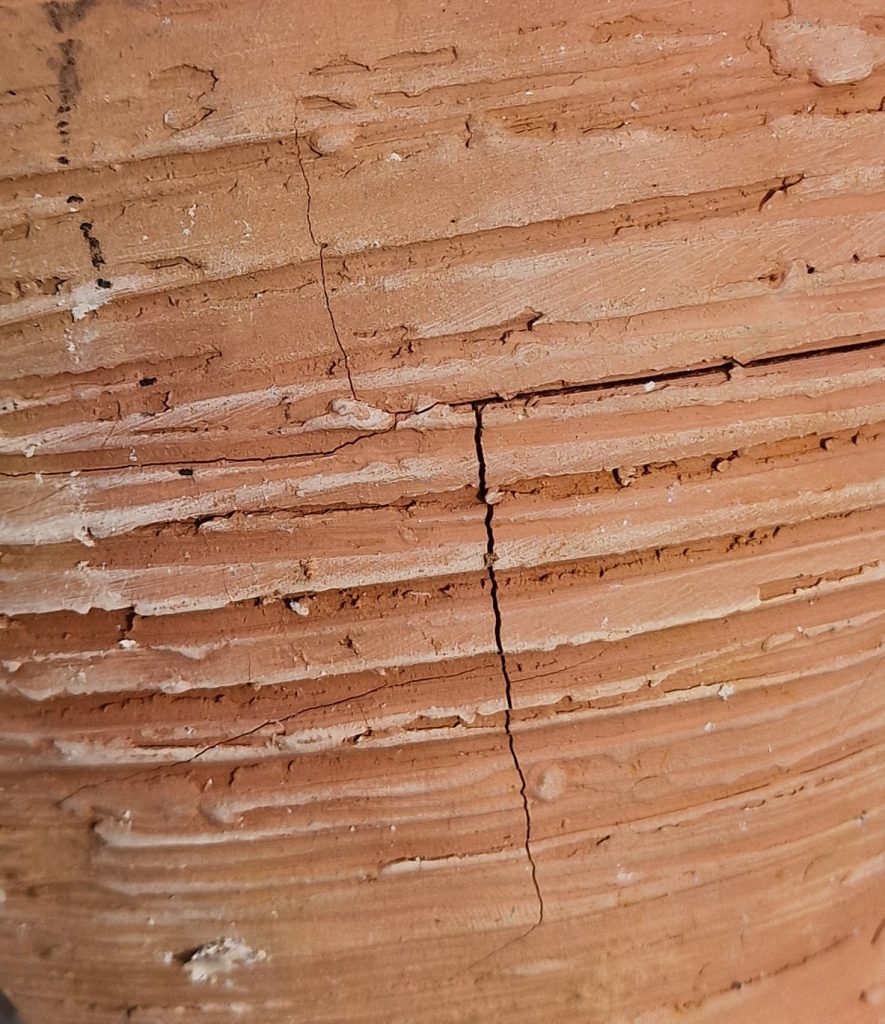
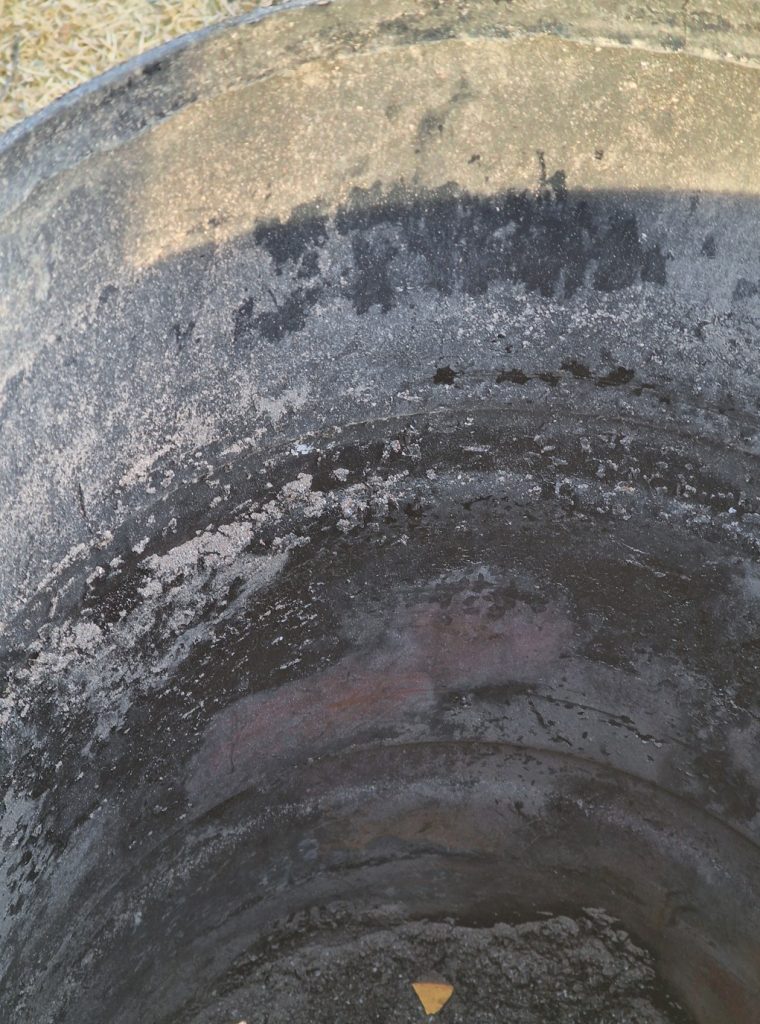
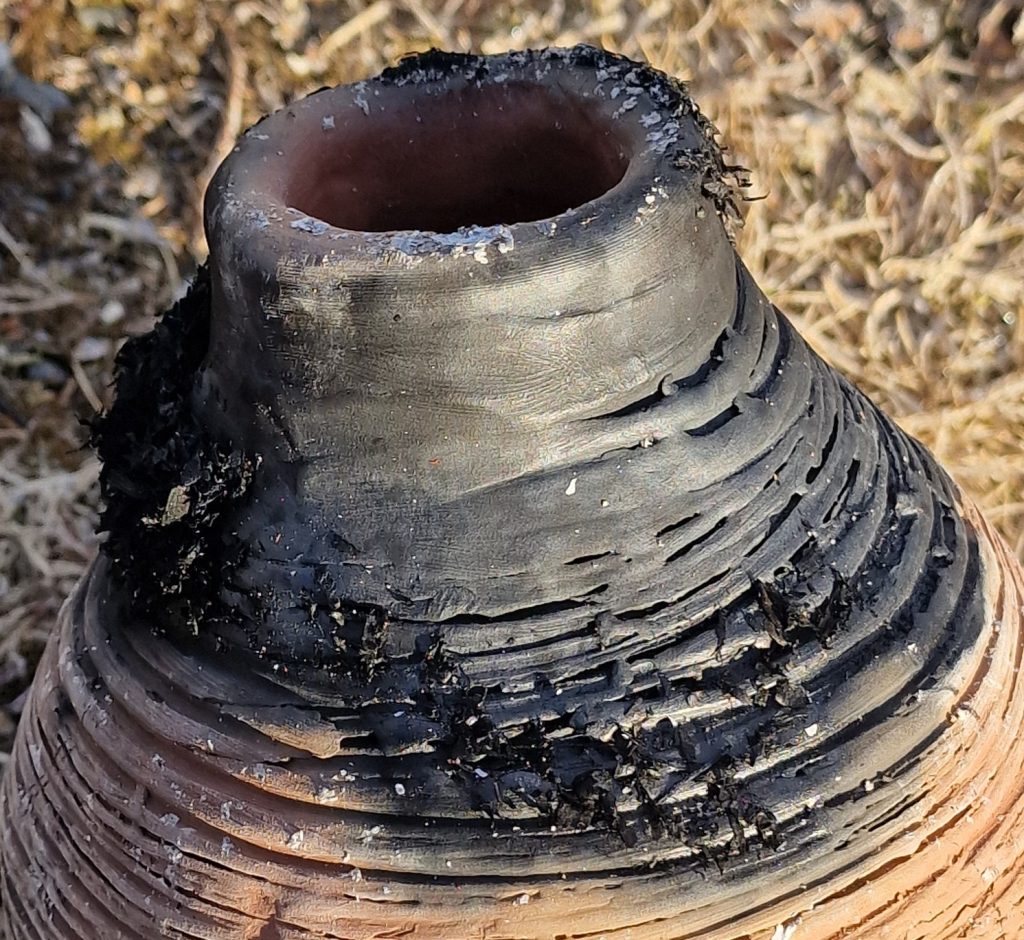
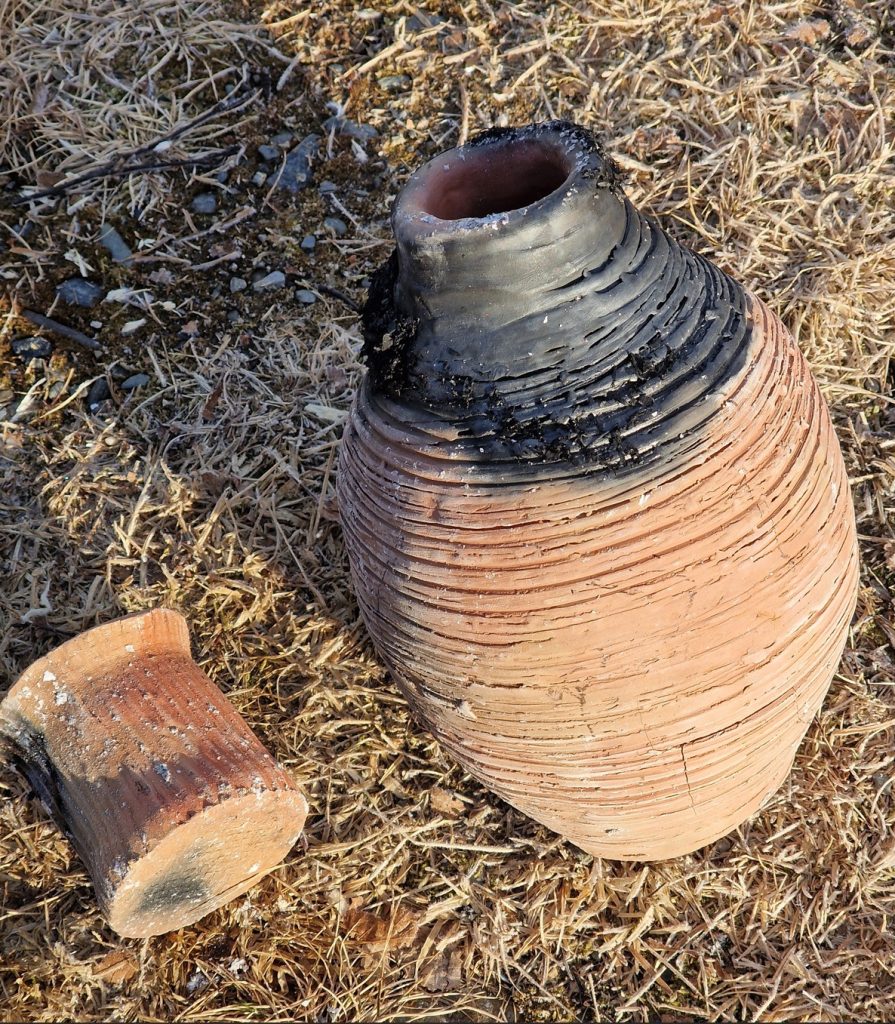
Did the oil drum burn stabile?
Did it get hot enough to make clay to ceramic?
Did the vessels get a black shiny expression?
Conclusion:
It’s used a small oil drum 65 cm high and 35 cm in diameter. A bigger one can take more pottery, need more sawdust, and can potesialy burn hotter. Sawdust firing is traditionally done in a loosely stacked brick kiln without mortar, “leaking” air between the bricks. The oil drum is fully enclosed.
At the start of the firing, there was no connection between the ventilation at the bottom and the fire at the top of the kiln. After hours of firing, the flames burned deeper into the oil drum and came into contact with the air vents in the bottom, which started to re-oxidise the firing process.
It should have been made fewer ventilation triangles at the bottom, and some few more should be made at the sides, this would make a more stabile kiln environment with little oxygen to the end.
The oil drum kiln burned extremely stabile with white thin smoke from the beginning to the end, the clay definitely turned to ceramic, so 600 + degrees Celsius was reached.
The re-oxidation at the end of the firing reversed the carbon-rich firing environment inside the kiln, but as a first test, the result was promising. Black pottery should be possible with less and better adjustment of the air supply.
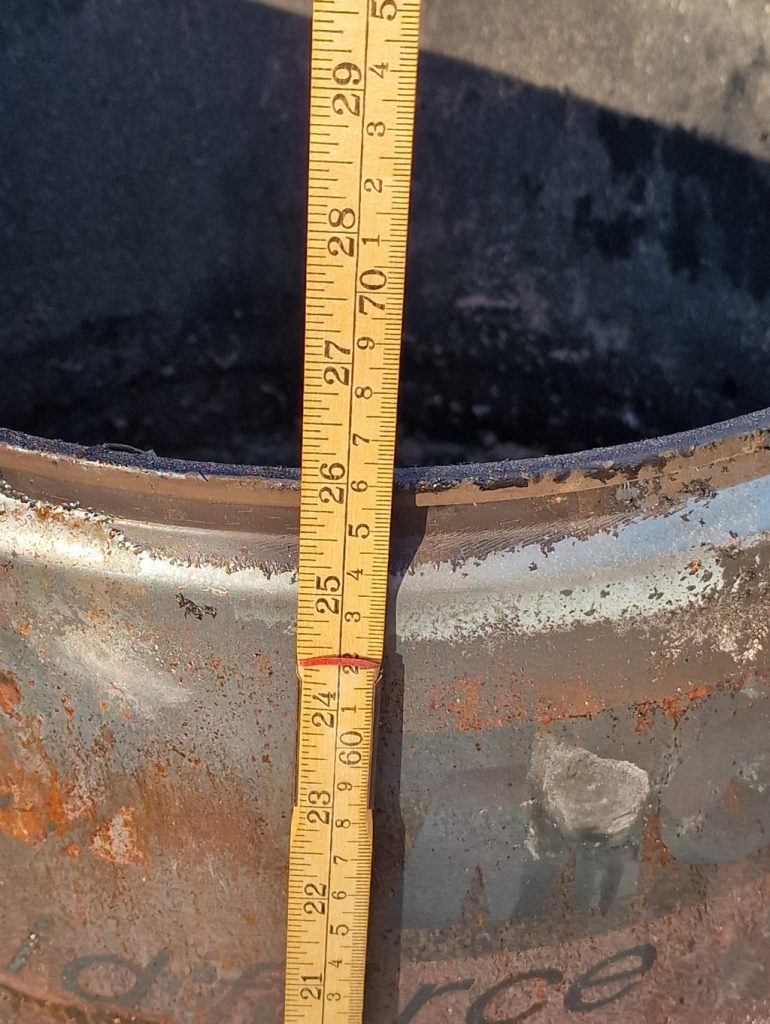
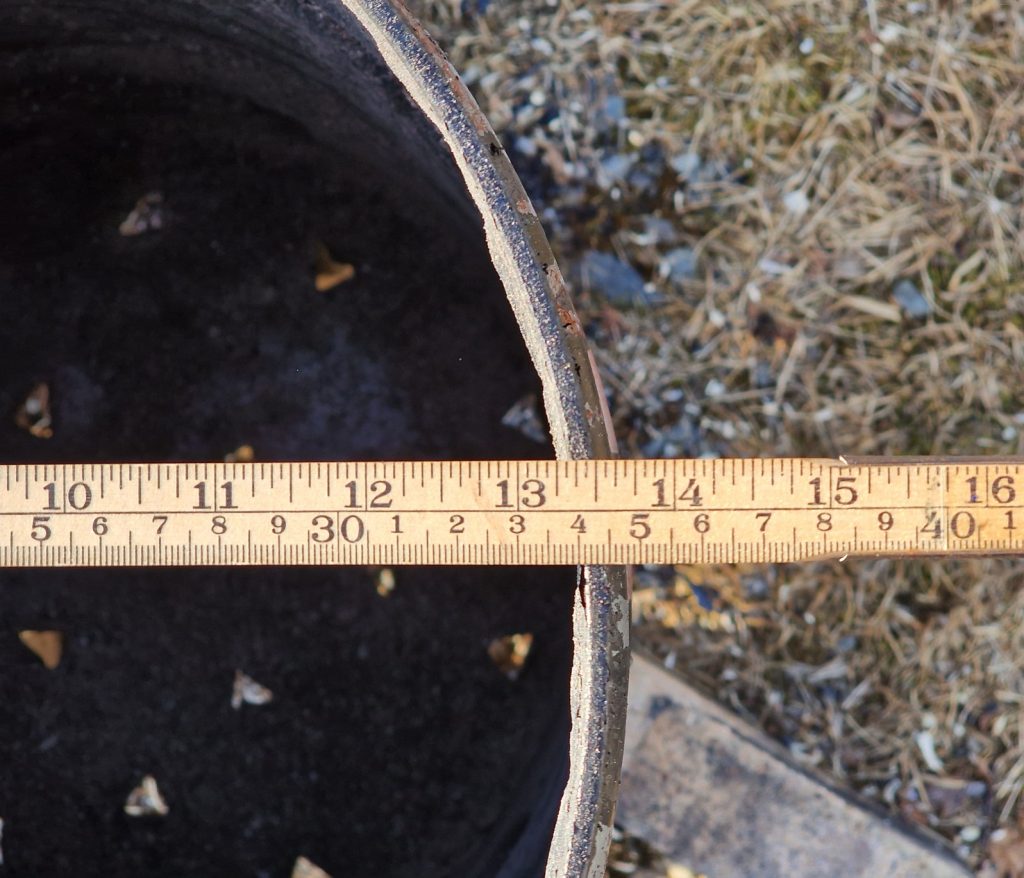
The small oil drum in this test is 65 cm high and 35 cm in diameter.
Also, check out the extremely low temperature DIY pottery glazes, they should work in the oil drum kiln:
Also see:
thepotterywheel.com/sawdust-kiln/